Making Transparent Bullet-Proof Glass Out Of Clay: A U.S. Naval Research Laboratory Innovation
The U.S. Naval Research Laboratory (NRL) has refined the process of making a special ceramic material called as Spinel that can serve as an alternative to conventional bullet-proof glass. Dr. Jas Sanghera who heads the team at the NRL says that spinel is actually a mineral called as magnesium aluminate. He also claims that the material is tougher, stronger and harder than glass and with the new manufacturing process that they invented the material can be moulded into any shape. This means they can be used, not just for military applications like armour but also for protecting consumer durables like camera lenses and smartphone displays. Conventional bullet-proof glass is made by pressing alternating layers of glass and plastic sheeting together and this prevents infrared wavelength of light. This means they cannot be used to protect a droneâs lens that has night-vision capabilities. The spinel however allows infrared light to pass through it, making it an excellent protection for UAV cameras. The team also says it can be fitted to the high-power military lasers that are used to obliterate missiles.
The team at NRL took ten years to develop a process called as sintering to make Spinel. Old methods for manufacturing spinel dictated that you had to melt the raw material, ceramic at temperatures of 2000 degrees centigrade. This was an expensive and energy hungry method and the NRL wanted to change that. The spinel made by the NRL is a polycrystalline material that is formed by pressing different types of crystal materials together. Sintering is the process of making spinel with the help of a hot press. The team put in the ceramic powder in a hot press under vacuum. The powder gets squashed together and the entrapped air is removed and the result is a clear glass-like material. To prevent cloudiness in the glass, the team added lithium fluoride which lubricates the powder particles to reduce friction and prevent the powder from moving around. If you want to improve the optics of the spinel, all you have to do is polish and grind the spinel just like you do with gems.
Dr. Sanghera says that the process is scalable and depending on the mould of the press you can make glass of any shape and size. The NRL is planning to license the manufacturing process not just to the Department of Defence but also to commercial manufactures.
Source: #-Link-Snipped-# via #-Link-Snipped-#
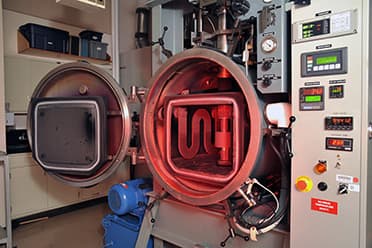
The team at NRL took ten years to develop a process called as sintering to make Spinel. Old methods for manufacturing spinel dictated that you had to melt the raw material, ceramic at temperatures of 2000 degrees centigrade. This was an expensive and energy hungry method and the NRL wanted to change that. The spinel made by the NRL is a polycrystalline material that is formed by pressing different types of crystal materials together. Sintering is the process of making spinel with the help of a hot press. The team put in the ceramic powder in a hot press under vacuum. The powder gets squashed together and the entrapped air is removed and the result is a clear glass-like material. To prevent cloudiness in the glass, the team added lithium fluoride which lubricates the powder particles to reduce friction and prevent the powder from moving around. If you want to improve the optics of the spinel, all you have to do is polish and grind the spinel just like you do with gems.
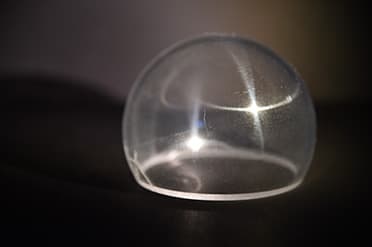
Dr. Sanghera says that the process is scalable and depending on the mould of the press you can make glass of any shape and size. The NRL is planning to license the manufacturing process not just to the Department of Defence but also to commercial manufactures.
Source: #-Link-Snipped-# via #-Link-Snipped-#
0