This Robotic Finger Looks And Feels Just Like A Human Finger
A team of researchers at the Florida Atlantic University led by Dr. Erik Engeberg, Assistant Professor in the Department of Ocean and Mechanical Engineering has been successful in developing a robotic finger that is very similar to a real finger. Developed using a shape memory alloy (SMA), a 3D printer, a 3D CAD model and a unique thermal training technique, this bio-inspired robotic finger derives inspiration from nature as well as biology to mimic the actions of a real human hand. Most robotic parts we see are restricted in terms of the range of motions and are rigid to touch. In this novel robotic finger, Dr. Engeberg and his team have mimicked the human finger's motions such as extension and flexion.
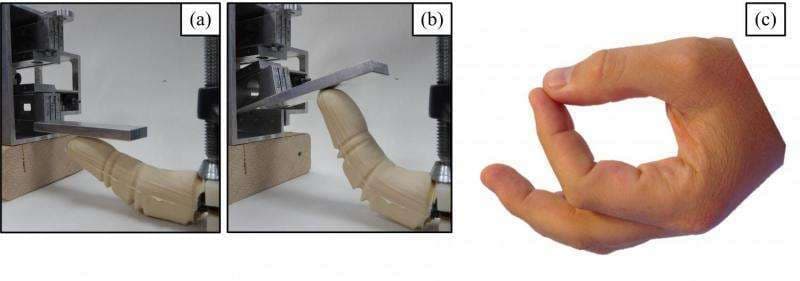
Robotic Finger from Dr. Erik Engeberg's Lab
The robotic finger has been so designed that it has a very light weight body as well as the dexterity required to show strength in motions such as grabbing, picking up, dropping and even pouring. With the range of movements that the robotic finger can perform, it is only obvious for the researchers to believe that it is ideal for use in a prosthetic hand.
The team used a 3D printer to create the inner and outer moulds, wherein the position sensors as well as flexor and extensor actuators were located. A novel resistive heating process known as 'Joule' heating was used, in which electric currents are passed through a conductor to release heat. The team's study showed that, upon heating the extensor actuator took a straight shape, whereas the flexor actuator took a curved shape.
A 3D CAD model of the human finger was used to create a solid model of the finger and SMA plates were used to assemble the finger using a multi stage casting process. They used an U-shaped electrical chassis for flowing the electric currents via each SMA actuator towards an electric power source located at the base of the finger.
This technology makes use of the heating and cooling process to operate the robotic finger. Since it takes long periods of time for the SMA to cool down, the researchers believe that it is best suited for applications in underwater robotics since it would have a natural rapidly cooling environment. Interestingly, the team's underwater experiments showed that the water cooling component greatly increased the operational speed of the finger.
Take a look at the team's recently released video where the robotic finger picks up and drops a can -
What are your thoughts about the novel technology? Share with us in comments below.
Source: #-Link-Snipped-#
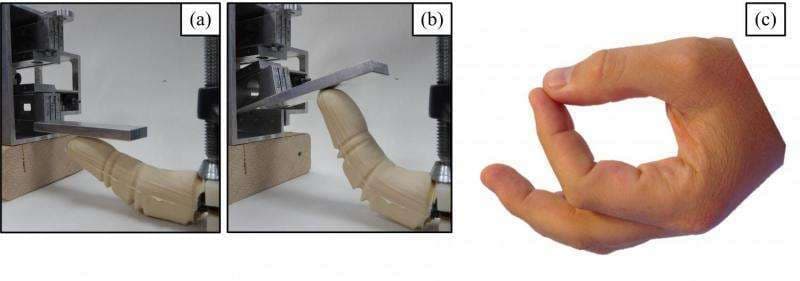
Robotic Finger from Dr. Erik Engeberg's Lab
The team used a 3D printer to create the inner and outer moulds, wherein the position sensors as well as flexor and extensor actuators were located. A novel resistive heating process known as 'Joule' heating was used, in which electric currents are passed through a conductor to release heat. The team's study showed that, upon heating the extensor actuator took a straight shape, whereas the flexor actuator took a curved shape.
A 3D CAD model of the human finger was used to create a solid model of the finger and SMA plates were used to assemble the finger using a multi stage casting process. They used an U-shaped electrical chassis for flowing the electric currents via each SMA actuator towards an electric power source located at the base of the finger.
This technology makes use of the heating and cooling process to operate the robotic finger. Since it takes long periods of time for the SMA to cool down, the researchers believe that it is best suited for applications in underwater robotics since it would have a natural rapidly cooling environment. Interestingly, the team's underwater experiments showed that the water cooling component greatly increased the operational speed of the finger.
Take a look at the team's recently released video where the robotic finger picks up and drops a can -
What are your thoughts about the novel technology? Share with us in comments below.
Source: #-Link-Snipped-#
0