Firstly I explain the
structure in brief. (figure 1)
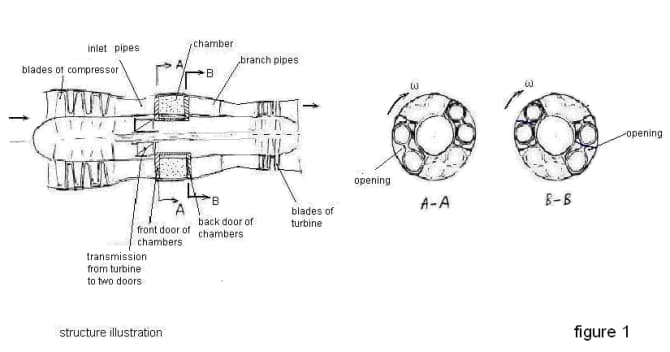
The left one is the section along axial, it show almost all main parts.
Another two pictures show the main parts: the front door and back door of the combustion chambers. two doors control and regulate work to complete combustion one by one. Anyone of combustion chambers sometimes sucks mixture gas; sometimes it the combustion happens inside it; sometimes gas exhausts from it. So the chamber sometimes is sealed by the two doors; sometimes it is open on both ends; sometimes it is open on one end. So the door has openings(slots) in it. The two doors rotate at same speed and co-operate each other.
As the amount of chambers, I draw 4 pairs, actually it will be more. It depends on the utilization rate of space; parts strength; stable work and other factors.
There is blower/compressor in front of the chambers. The branch pipe, turbine install behind the chambers. There may be also branch pipes in front of the chambers to input gas but they are very short so that they are not illustrated in the upper pictures
Now I state the work procedure.
Let us review the current jet engine's work procedure: the first step is that compressor suck air and increase the pressure to high level, the air enter combustion chamber, be mixed with fuel, burning, during the course the pressure remain consistent in chamber; after complete burning, gas goes out of chambers and drives turbine; turbine transmits the power to the compressor ahead; at last the gas utilizes the rest energy to accelerate itself to push jet engine.
In my design: The first step of jet propulsion's work procedure is that the blower suck air and increase it to proper pressure, mix fuel as well; then through a pipe the gas enter the combustion chambers, after the front door and back door close, then burning inside chambers and the pressure increase rapidly, the back door open; the gas run into the branch pipes; then general pipe, there is a turbine afterwards to get power for the blower/compressor ahead. After the branch pipe the gases converge, flow out off the engine so as to give whole engine a consistent push force.
Upper I state two work courses, there is another course, at the end of the spouting course, the front door of chambers opens, and the fresh gas enters meanwhile drive/sweep the waste gas out off the chambers. So the chambers spout gas alternatively. All courses are controlled by chambers’ front door and back door. In common case, there are always a couple of chambers at the same course. All chambers are arranged as a circle. The section shape of chamber is round or close to round.
The combustion in each time needs several milliseconds to complete. Though it is so quick, if the rotary doors are driven by turbine, you should reduce the rotation speed from turbine to the valve. The speed of turbine is too high for doors because the combustion needs time. A transmission unit is needed from turbine to doors.
(or by pneumatic solution to realize)
Because the combustion of each time can within tiny little time, practically it is not necessary that chambers are closed completely at both sides during combustion course inside the chambers as far as we can get almost same high pressure gas. In this sense we also can call it
the constant-volume combustion type.