Boiler & Furnace
The latest company which makes hand made paper has asked me to look at two main areas where they are losing a lot of energy/money.
The first is the boiler. They use the steam channelled through radiator's that they hang the paper on to dry. I believe the boiler to be a water tube boiler (it has a vertical design) on a open system (the water is not returned directly to the boiler). Firstly I noticed that neither the pipes or the boiler is insulated, Now they could save a truck load of energy by insulating, I'm right in thinking fibre glass is the way to go with steam pipes and boilers? and how do I work out the thickness needed?
The other area Is the Furnace they currently heat up 3 vats of water with the raw material in to make it softer and ready to be used to make paper. But the last station is receiving very little heat. After observing the process I noticed huge amounts of heat being lost out the top of the first vat (and probably the second but it wasn't full) as steam because they never seal the lids properly in case the vats explode. I think they should look at some sort of pressure cooker design and seal the vats properly to make them more efficient, what do you think? would this just be a case of adding a pressure release valve?
I have attached some photos to help get the feel of it.
![[IMG]](proxy.php?image=http%3A%2F%2Fwww.engineersedge.com%2Fengineering-forum%2Fimages%2Fsmilies%2Fsmile.png&hash=563bbb5717a829905d11a629d41f04c1)
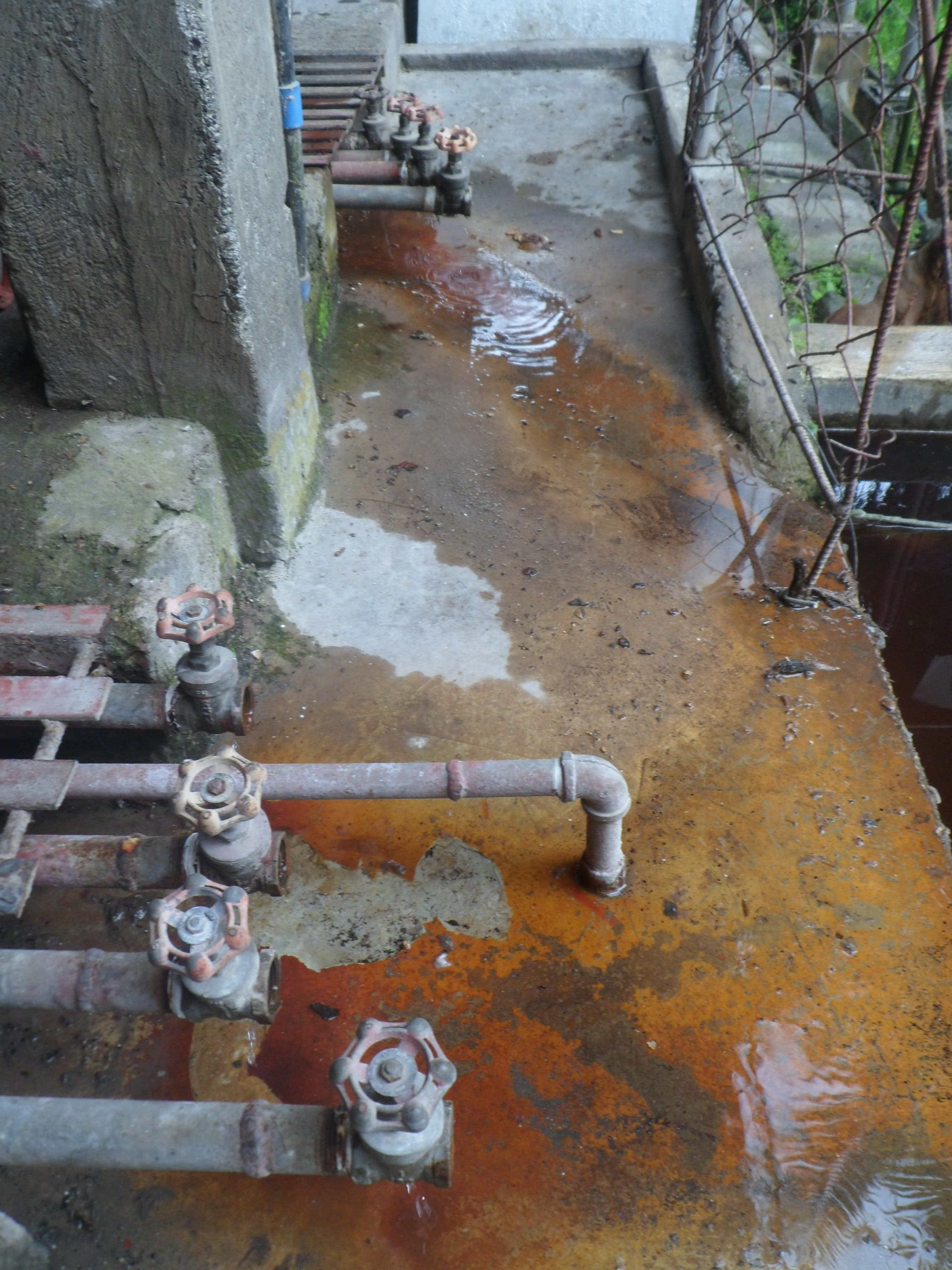
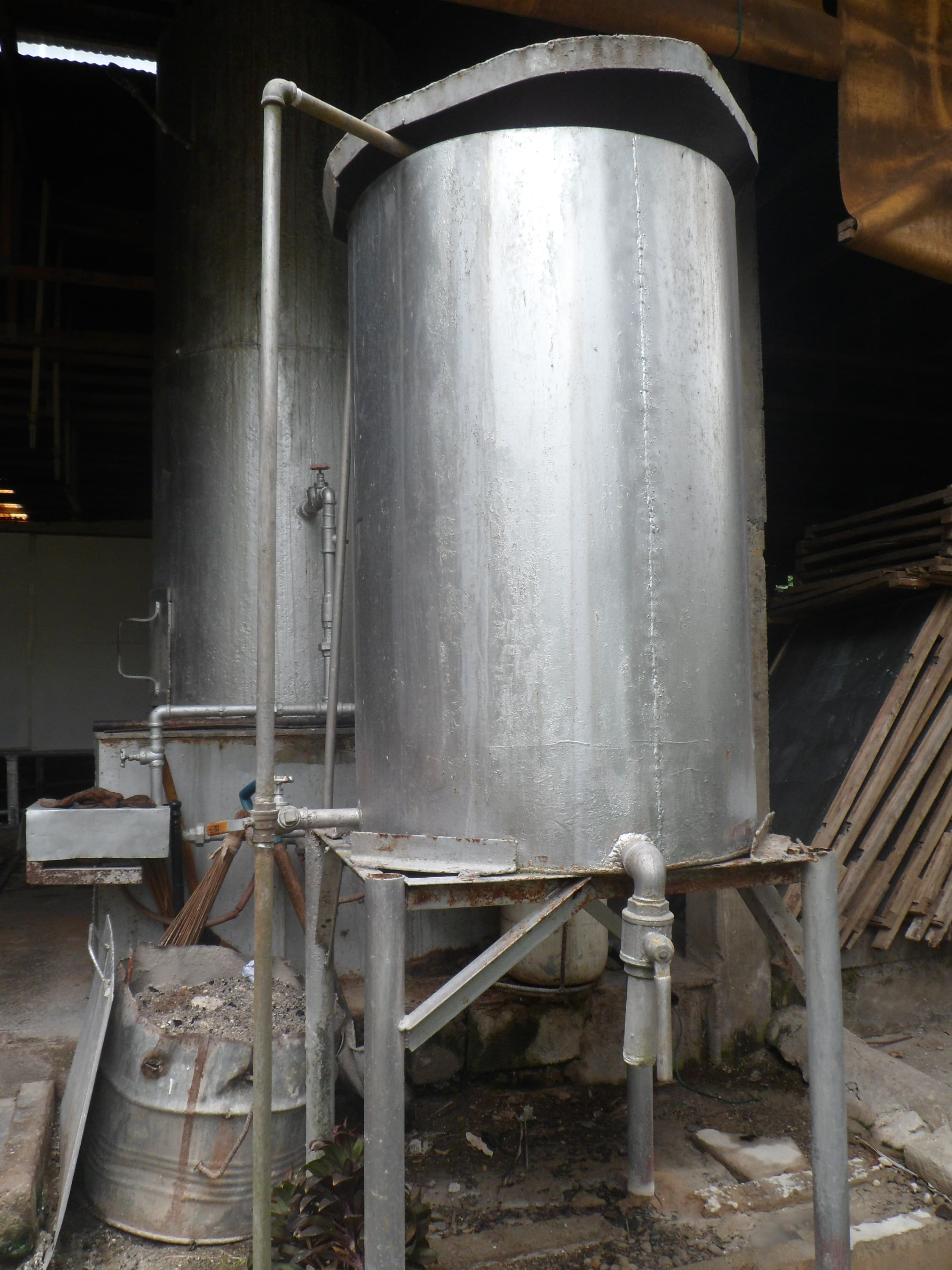
I would appreciate any help or ideas on this, maybe even just a line of research for me to head down. Many Thanks Hammer.